クリーム容器・アトマイザー
一貫生産体制
一貫生産体制で、「低価格」「短納期」「安定品質」を実現。
競争力の高い製品づくり。
当社では、仕入れた原料を加工して、製品として完成させるまでの、ほぼ全ての工程を自社で行っています。
これにより、協力工場との分業であれば生じる製品部品の輸送日数、打ち合わせ時間、加工日数を大幅に削減することができ、「短納期対応」を可能にしています。
また、すべての作業が自社内なので生産ラインを調整しやすく、お客様のニーズに応じた小ロットの生産、急な仕様変更、数量変更にも迅速に対応することが可能です。
さらに、品質管理を一貫して徹底管理することで、「安定した品質」でお客様にお届けしています。
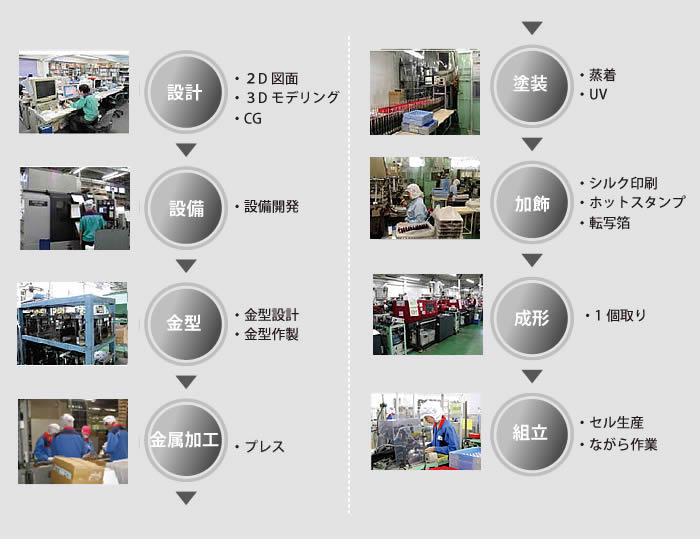
※もっとくわしくは「工場見学」のページをごらんください。>>こちら
生産設備の内製
コスト削減と、自社で解決できる技術力・対応力の育成。
当社では「必要なものは自分たちで作る」を合言葉に、設備や治具の内製化を行っています。
工場内にEG(エンジニアリンググループ)があり、工場の生産設備の設計・開発・メンテナンスを自社で行い、市販の設備では出せない生産性や加工精度を実現できるようにしています。
また、必要十分で余計な機能のない設備を製作することにより、設備にかかる費用を必要最小限におさえ、社外に委託する場合の1/10までコスト削減できています。
さらに、社内でメンテナンス・改良がスピーディにできるため、社外に委託するよりも納期を早めるというメリットもあります。
これらはコストの削減だけを目的にしたものではありません。設備を内製することによって、設備構造や特性の理解、技術の伝承と技術力の強化を図り、社内の技術力・対応力を維持・向上させるはたらきもしています。
改善活動
問題意識と発想で改善。収益を営業だけに頼らない体制づくり。
当社では、作業の効率化を目的として、方法改善と設備改善の二段階で、徹底的な改善をはかっています。
方法改善
部署ごとに、方法改善のためのミーティングを毎週実施しています。社長と従業員の全員参加です。
そこで人員部分で対応可能な効率化を徹底追求して、作業手順や機材の配置などにより改善をはかります。
設備改善
方法改善を尽くした上で、それでも尚効率化が必要な部分については、十分に精査した上で必要な設備を導入しています。EG(エンジニアグループ)からだけではなく、生産現場から設備のアイデアが上がることもあります。全員でアイデアを出し合い、最善の方法を引き出しています。
従業員ひとりひとりが常に主体的に問題意識をもち、解決のためのアイデアを出して問題解決に向かっています。これは、作業の能率化に留まらず、新しい製品づくりのアイデアや問題解決力を高めることにつながっています。
また、こうした改善活動によって生産側で最善をつくすことにより、収益を営業だけに頼らない努力をしています。
ヒダン式ものづくり
1.造るタイミング
造ってできたものを売るという考えではどうしてもムダが発生してしまいます。売れるものをタイミングをはかりながら造ることで、在庫をなくしムダを省きます。
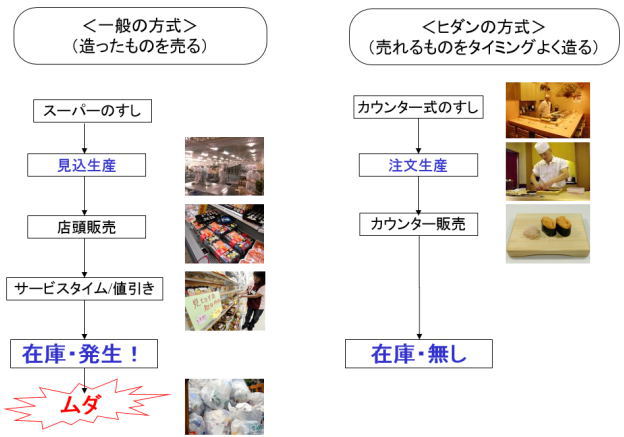
2.人の動き
原則的には機械ができる事は極力機械で、人が出来る事だけを人がやっています。しかし機械が動いている間には人が入り、その隙間時間を無駄にしないように、別の作業が行える配置にして、効率性をアップさせています。
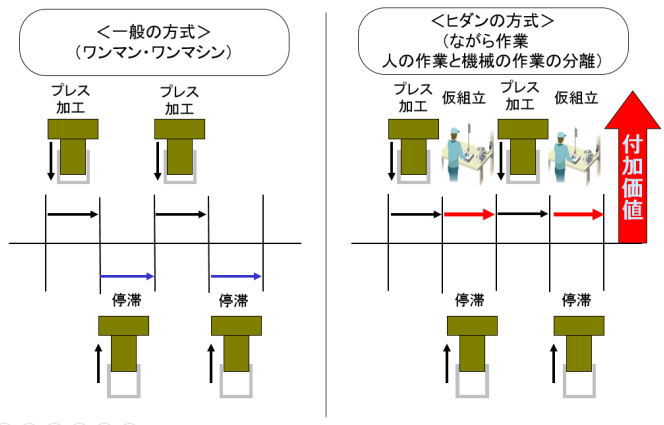
3.設備の規模
大型の機械を入れて大量生産するのではなく、小型機械を多数入れて生産しています。機械が故障した場合でも、すべてがストップすることなく、生産を続けられます。また、金型や治具の交換・段取り替えも、必要な台数に合わせて効率よくできるというメリットがあります。
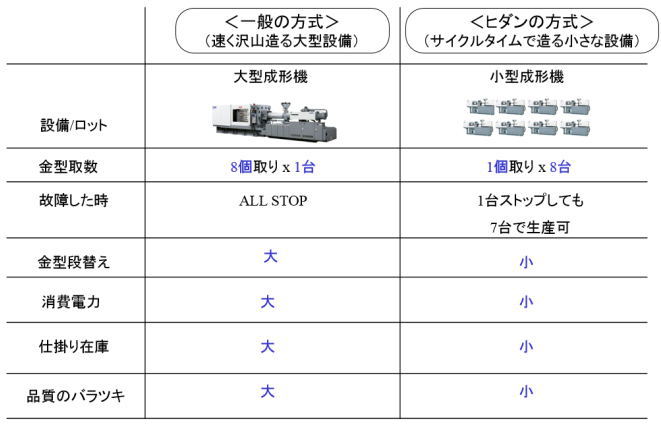
4.工程の流し方
作業者一人ひとりが多工程を受け持ち、1個造りを基本としています。1つ1つ細くて速い生産ラインを、多数作ることによって、通常の大量生産と同じ生産力を形成しています。これにより、完成までの日数を短縮できたり、作業変更の場合のリスクを少なくできたり、完成まで受け持つことで作業者の責任感とモチベーションを高めたりすることができます。
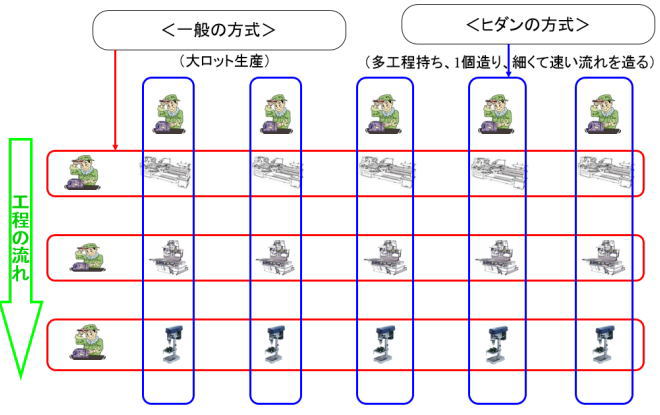
5.能率の考え方
たとえば生産能率を25%アップするという目標を掲げた場合、現状のまま生産力を上げても生産量に無駄ができてしまうことがあります。生産効率だけに着目するのではなく、目標を必要数に合わせた上で、人員で25%分をカットし目標達成をめざします。
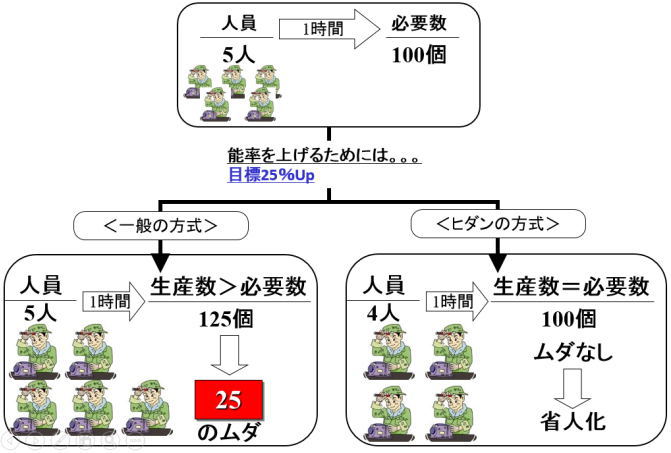
6.品質の確保
人の目による検査では、どうしてもミスを見落とす可能性が出てきます。検査の部分を機械化することで、精度の高い検査を実行し、作業工程にポカヨケを組み込むことによって、無駄な工程を省いています。
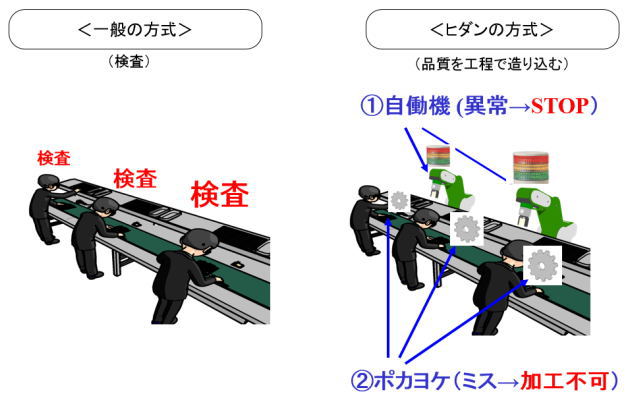
7.改善の組織
改善活動は一部のスタッフによる限られたテーマで実施されることが多いのですが、当社では従業員全員参加で、広く意見やアイデアを拾って、小さな改善も無視せず行っています。この積み重ねが最大の効率化を生み出し、働きやすさにもつながっています。
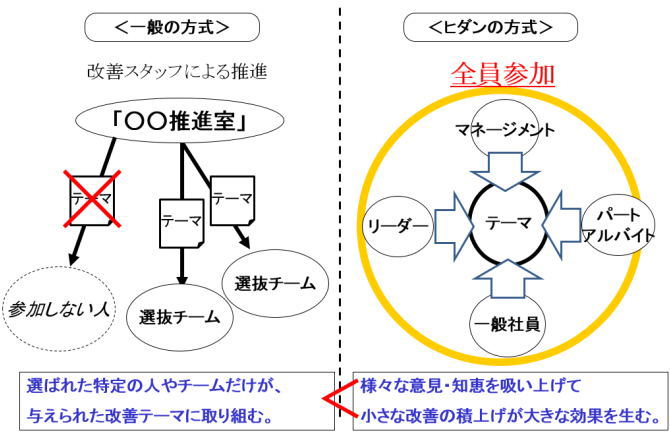
工場見学
会社概要
社名 | 株式会社ヒダン |
---|---|
英文社名 | HIDAN CO.,LTD. |
代表者名 | 松沼 英雄 |
所在地 | 〒130-0014 東京都墨田区亀沢1-5-13 |
TEL | 03-3624-1134(代) |
創立 | 1950年 |
資本金 | 1億円 |
従業員 | 国内310名 海外750名 |
事業内容 | 化粧品容器の製造、及び販売 |
取扱品目 | 繰り出し容器(金属、樹脂)、蓋物(金属、樹脂)、中皿(金属、樹脂)、アトマイザー、金属コンパクト |
ACCESS MAP | ![]() |
---|---|
お知らせ |
株式会社ヒダンでは「一般事業主行動計画」を策定し、
|
沿革
1937年 | 東京都墨田区に株式会社富士商会を設立 化粧品の金属加工容器を生産開始 |
---|---|
1950年 | 株式会社飛弾製作所に改組 |
1964年 | 千葉県柏市花野井に工場を建設、操業開始 |
1970年 | 柏に本社業務を移転 |
1971年 | アルマイト工場棟を完成、シルクスクリーン印刷設備を導入 |
1990年 | 大阪営業所を開設 |
1991年 | 株式会社ヒダンに改名 |
1993年 | 中国昆山経済技術開発区に飛弾化粧品容器(昆山) 有限公司を法人登記 |
1994年 | 昆山経済技術開発区に生産工場の建設を開始 |
1995年 | ニューヨークにヒダンアメリカ設立 |
1996年 | 昆山工場にてHIDAN同期生産ラインシステムの操業 |
1997年 | パリにヒダンフランス設立 |
2002年 | 昆山工場ISO9001取得 |
2003年 | 船橋新工場完成 柏工場より移転 |
2003年 | 昆山第2工場完成 |
2007年 | 化粧品製造販売業及び製造業認証取得 |
2008年 | 昆山工場UV塗装設備、蒸着設備導入~稼働 |
2011年 | 昆山工場ISO14001:2004及びOHSAS18001:2007を取得 |